Our Services
As a market leader in foam core machining, our staff are adept at meeting the diverse needs of a broad range of sectors that depend on high quality advanced composite components.
Our services range from CNC machining through to the manufacture of complex composite parts using pre-preg materials and autoclave cure. Our engineers and technicians specialise in making intricate parts from materials that include, but are not limited to, ROHACELL®, Airex and Diab foams.
We benefit from a well-stocked warehouse so we usually have clients’ preferred materials on site, allowing us to make parts swiftly and without the drawbacks of waiting for overseas deliveries. We hold wide range of ROHACELL® foam material from the basics like IG-F-31 through to IG-F-110 to the more exotic like ROHACELL® WF110 and WF110-HT, to name a few.
As our certifications demonstrate, we can trace the process, materials and technicians involved in all stages of manufacture. Clients value this quality assurance and we enjoy large levels of repeat business.
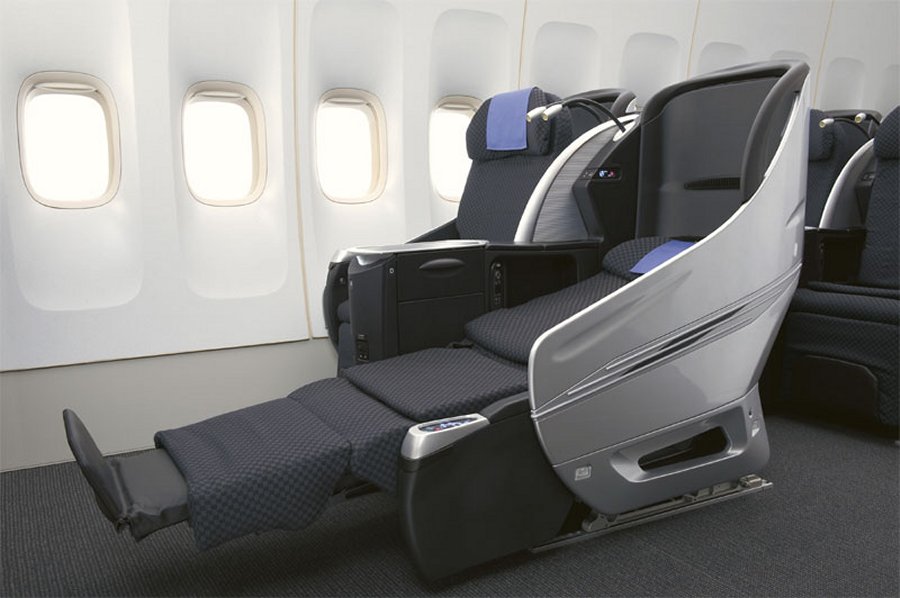
If you are seeking a fresh, professional service in the advanced composites’ market, we would enjoy meeting you, introducing our team and showing you around our facilities.
Our engineering team can bring your ideas to life, with many years of experience of composites and state-of-the-art computer CAD systems, tooling and models can be experimented with prior to cutting material allowing the customer to see for themselves the final product.
Each project is handled by an experienced project engineer who liaises with the customer – working with them to refine the design. The tooling can then be generated either by hand or more likely on one of our CNC machines.
We take a great deal of effort to keep the customer involved throughout the process generating prototypes as required before finally putting the part into production.
With our many years of experience in working on modern sailplanes combined with our ability to machine parts on our CNC routers we were asked to create a full size models for the A400M engine nacelle by GKN Aerospace Test Facilities.
Using CATIA model data and importing it into our CAM software we were able to cut accurate skin profile in block foam before skinning with a mixture of glass and carbon fibre fabrics.
By combining the accuracy of CNC machining with traditional hand skill the model was brought to life. All aspects of the work were completed within our own workshops allowing us to control the overall design and construction methods. The final model had an overall length of 3.5 mtrs and a width of 1.25 mtrs. When checked for accuracy using CMM methods it was confirmed to be within 0.5% of drawing.
The project took us just over 4 months to complete from initial receipt of CAD models to delivering it to the customer.
This high profile project for a major Aerospace customer demonstrated Severn Valley Sailplanes ability to carry out large scale projects within budget and a tight time frame.
We have a large heating platen measuring 1.2m x 0.9m capable of heating RohaCell sheets to their thermoforming temperature of around 190°C. This allows many shapes to be formed without the need for extensive machining.
In addition we have a strip heater 0.9m x 0.05m that has proven useful for simple work. To complement the heating platens we have several ovens for drying material.
There are several foam core materials on the market today that are capable of being thermo-formed into relatively complex shapes. Two of the market leaders are ROHACELL® and Airex. Whilst these foams are quite different they both have the same basic characteristic in that when heated to a set temperature they are capable of being formed and upon cooling will keep that form.
Airex can be formed at quite low temperature (about 100 deg C) where as ROHACELL® requires a higher temperature (180 – 200 deg C) but has the advantage that it can be autoclaved at 120 deg C as part of a conventional co-cure operation.
As specialists in this field we have developed a range of bespoke thermo-forming machines capable of manufacturing most parts.
For further information of this manufacturing process please contact us.
To help you understand the benefits of thermoforming better we have put together a short video showing the process.
The requirement to thickness core material to close tolerance is a much sort after process and we have equipped our workshop with two sanding machines capable of achieving close tolerance specifications in a range of core material.
Using similar machine to those used within the core manufacturers own facilities we can achieve accuracies of better than +/- 0.2 mm on full sheets and better than +/- 0.1 on quarter width and smaller sheets.
The ability to accurately sand to these tolerances opens the door to using Rohacell HF material for many spacing and holding applications within the electronics and antenna fields where this material has good radiation transparency characteristics.
As with many other areas of the business we can tailor the product to suit the customers needs and can work closely with customers to produce small sheets sizes to very high tolerance.
Our large format sander can work between 150 mm and 4 mm with an accuracy of +/- 0.2 mm
Our quarter sheet format sander can work between 80 mm and 0.8 mm with an accuracy of +/- 0.1 mm
If you have a need for this service please contact our sales office staff.
For the past 4 years we have been involved in the manufacture and machining of foam cores for some of the worlds leading airlines such as British Airways and United Airlines. Our manufacturing techniques have put us at the forefront of the changes taking place in Business Class travel on the worlds airlines.
From our facilities in Gloucestershire our team of technicians have developed pioneering manufacturing methods to bring these exciting shapes to life within the tight budgets demanded by our customers.
We have invested in state-of-the-art CNC machinery including: a CMS Athena 5 axis CNC Router for most demanding projects. we also run 4 large format high speed CNC table routers each capable of accepting full sheets of core foam.
To supplement our machinery our workshop staff have many years experience in finishing and the production of parts using more traditional hand methods. In all we offer a complete service for our customers.
We are able to accept drawings in most formats such as IGES, STEP, DFX, DWG and many others, please feel free to contact us to discuss your exact requirements.
Each type of core material has unique properties allowing specialised uses, for example Rohacell HF’s is often used as a spacer or filler within aerial and RF circuit designs.
Using precision sanding and milling methods complex shapes can readily be cut to remarkable accuracy. We have invested in a quarter sheet sander capable of machining down to 0.8 mm thickness. While foam at this thickness is like card and not generally used in composites it is used for precision spacers in antenna arrays and other electronic products. We can supply matieral at any desired thickness between 0.8mm and 8.0mm to a tolerance of +/- 0.15 mm (+/- 0.1 mm on request) across a small sheet (typically 625×415 +/- 2 mm) and the results are very impressive.
In today’s world of manufacturing we rarely see paper drawings as most of our customer work in a variety of CAD drawing packages.
We operate seats in both MasterCam and OneCNC both of which are current releases allowing us to accept models in the vast majority of formats.
Our CAD operators have many years experience in taking customers designs and turning them into final product.
Please contact us for full details.
We operate a small autoclave suitable for low volume proto-typing or production work.
Using computer linked controller we are able to monitor and record the complete curing cycle for later analysis and quality control.
For use solely with pre-preg materials the autoclave combines pressure and vacuum to produce consistent, highly detailed parts.
We pride ourselves on the rapid response we offer, and have experience of meeting the tight deadlines demanded of today’s customers.
To ensure customers requirements are satisfied and to control quality within our workshops we have invested in a Romer Omega CMM measuring arm. This 3 meter arm is capable of measuring to well within 0.1mm over the complete radius of the arm allowing even the largest components to be checked against models, drawings or data.
We run Delcam Power Inspect software: one of the best products on the market and our technicians have been fully trained in its operation by Delcam. The purchase of the arm was a major investment but the benefits in terms of improved quality of product have paid dividends. Our customers especially appreciate the detail of the reports produced.
Customers can be assured that where required we can verify compliance to drawings or reverse engineer components to levels of accuracy to match the most demanding of applications.
The skills needed to repair composites are far different to those required when manufacturing. For the past 20 years we have been repairing complex composite structures.
Our workshops can tackle all types of repairs, from minor dings through to major tub damage. Using pre-made autoclaved patches we can return such complex structures back to service.
We also understand the time constraints customers are under and will try hard to return repairs within those limits.
Whatever your repair needs please give us a call and then relax in the knowledge that the work is being untaken by “professionals”.